Nidaplast Honeycomb Core
Nidaplast is an
extruded polypropylene honeycomb material for use as a light weight core
in composite sandwich panels.
The core density is a low 80 kg/cu m.
It features a non-woven polyester scrim thermofused onto each of
the core faces, which provides superior bonding properties and peel
strength. A polyethylene film
is fused between the non-woven scrim and the honeycomb in order to
minimise resin migration into the cells of the honeycomb.
Nidaplast
provides good strength, exceptional resilience and material integrity in
cored composites.
The thermofused polyester facing scrim ensures a non-peelable bond
to the ends of the honeycomb cells, which avoids the perpetual problem of
glued honeycomb composites which rely exclusively on the very small amount
of adhesive which can bond the skin to the cell walls.
The polyester scrim is compatible with all laminating resins -
polyesters, vinyl esters, epoxies, and acrylics.
Composite panels may be prepared by laminating face skins of many
materials - fibreglass, plywood, aluminium, etc.
The polyester scrim requires approximately 400 gm per sq m of resin
to fully saturate and bond to it.
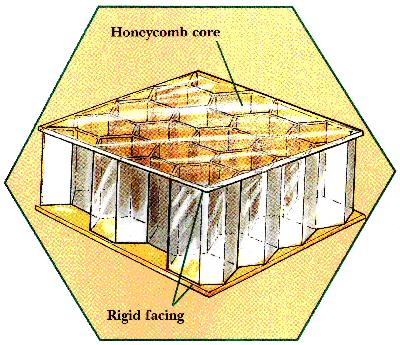
The
polypropylene core of Nidaplast has a Heat Deflection Temperature of 105
deg C, therefore Nidaplast composites are not prone to softening in direct
sunlight. Its flexibility is
beneficial in enabling curved structures to be laminated in situ, such as
crowned decks, curved cabin sides, etc.
It has very good impact resistance and fatigue resistance due to
this flexibility.
As a
non-reticulated honeycomb there is no possibility of water penetration
spreading throughout the composite subsequent to any localised damage.
It is totally resistant to water, mild chemicals, and solvents.
Nidaplast has excellent thermal and acoustical insulation
properties, and acts as an efficient constrained layer sound damping
medium.
In comparison
with commonly used PVC and similar foams, Nidaplast shows similar values
for compression strength and slightly lower values for shear and tensile
strengths. Being more
flexible, it has lower stiffness (modulus) properties.
In turn, foams have much lower properties than end grain balsa also
used for cores. Therefore
design and application of composites using Nidaplast must take into
account these parameters.
Nidaplast has
the following approval from Bureau Veritas:
“Application / Limitation of use: Decks, superstructures, and accomodations for yachts, fishing vessels, service and working ships, and inland boats according to the Society’s rules”.
“Application / Limitation of use: Decks, superstructures, and accomodations for yachts, fishing vessels, service and working ships, and inland boats according to the Society’s rules”.
Nidaplast cores and Coretech panels offer the most cost effective, versatile, lightest weight panels currently available for marine and transport applications.
No hay comentarios:
Publicar un comentario